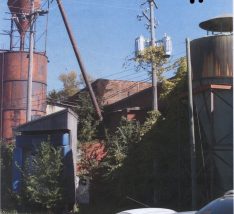
Demolition Photos From Early 2000’s
I love any demolition pictures. You know what they say, “a picture is worth a 1000 words,” so, I will not  be saying much. It is difficult to remember what a mess this place was, added on spaces to other added  on buildings. What a mess.